Manufacturing Case 1
Equipment: Pump
Name of the Part: Sleeves and Plungers
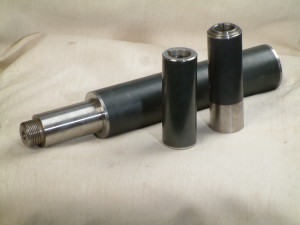
Plunger and Sleeve
Present Problem: A major expense associated with pump operation is replacement of sleeves/plungers. Wear on these components necessitates:
- Frequent packing adjustment to compensate for dimensional changes caused by wear.
- Packing material failure due to sleeve surface roughness.
- Premature pump stoppage due to leaks.
Cause Of The Problem: Abrasion, Corrosion and friction.
Our Solution: Provide a long lasting wear resistant surface of ceramic oxides or metallic carbides. We have a robotic Plasma transferred arc system (PTA) and flame spray equipment to apply coatings of tungsten carbide in a nickel chrome boron matrix and chromium oxides. The coating thickness is selected based on application wear potential and varies from 0.5mm to 1.5mm in thickness. For severe wear applications PTA coated sleeves last longer.
Industries in which these are used: Thermal power plants, Sugar industries, Oil and gas sector and chemical process plants are major consumers.
Manufacturing Case 2
Equipment Part: Bead Mill Disc
Bead Mill Disc
The problems faced in
Bead mill plates are subjected to abrasion and mild impact caused between continuously striking Zirconia bead and finely powdered product.
The main cause of this problem could be the Zirconia beads and powdered product are abrasive in nature. The MOC of the bead mill plate selection should allow a combination of elasticity and hardness yet reduce zirconia bead breakage.
The Solution that we provide in this case is that Bead mill working parameters were set to reduce zirconia bead breakage. Bead mill plates were manufactured as follows:
(a) SS 410 forged ring was welded to an alloy steel plate. Subsequently the fabricated plate was machined to required dimensions.
(b) Polyether based polyurethane of 3 to 5mm thickness was injection moulded or cast on the pre fabricated plate. P.U. has a hardness of 90 Shores.
Manufacturing Case 3
Equipment Part: Atomiser Wear Part of Wheel Disc
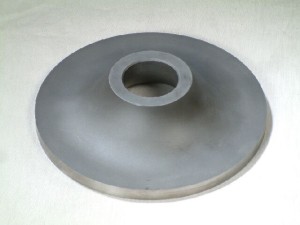
Top View of Atomiser Disc
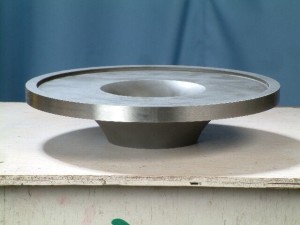
Front View of Atomiser Disc
Wear part is made out of Boron Carbide material, which is a kind of ceramic material and is brittle in nature. The raw material impinges at a very high velocity on a rotating disc. The resultant erosion thins the Boron Carbide till it suddenly break in to the pieces. The disc is rotating at 24,000 RPM and the sudden breakage causes heavy damage to other parts.
Main cause of wear is erosion at a temperature of 540 C along with centrifugal force due to high rotational speed. The impinging material is hard and has a tendency of caking. This reduces some wear but increases imbalance that may cause vibration and subsequent failure due to variance in centrifugal forces.
Our Solution that we provide is that
Boron Carbide was replaced by wear part made of machinable and harden able Titanium Carbide. This material can be processed more easily to manufacture this rather complex profile. TiC isn’t brittle, has high erosion resistance and retains hardness at an elevated temperature of 540 C. The low density doesn’t induce stress on the bearings of the wheel disc that is rotating at 24000 RPM. This application has now been standardized. The wear part is inspected every month during the routine maintenance schedule to study the thinning and to decide on replacement period. The end user managed to save a huge amount of money because of avoidance of sudden break down and unscheduled shut down.
Manufacturing Case 4
Equipment: Atomizer
Name of the Part: Insert (Nozzle)
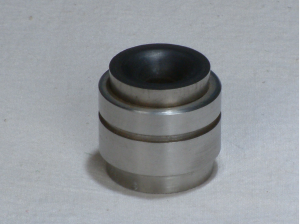
Atomizer Wheel Disc Insert
Present Problem: Insert was made out of Boron Carbide material, which is a kind of ceramic material and brittle in nature. Due to its brittleness it gets broken many a time while handling as well as unexpected impact load in the process. Thus life of each insert was uncertain and not possible to predict for maintenance department. Sudden breakage was acting as a main cause for downtime.
Cause of the Problem: Main cause of the problem was material that had been utilized to make the component. Boron Carbide was suitable material to combat the wear but due to it's brittleness it couldn't perform as per the mark. Therefore demand was such that material would have wear withstanding compatibilities along with metallic base so it couldn't break anywhere in process cycle.
Our Solution: Boron Carbide was giving remarkably good life if it wouldn't break in between. Apart from eliminating breakage factor we had to maintain the present life then. We conducted several trials with different grades of carbide materials those aren't brittle. We concluded on sintered Titanium Carbide (TiC) material in tool steel matrix. TiC offers constant wear rates with out breakage for the same period of time. Due to low density of TiC it appears as economical solution too in long run. We developed the procedure to manufacture insert with in very short delivery period.